Future Trends in Precast Concrete Technology
Precast concrete technology has undergone remarkable advancements, positioning itself as a cornerstone in modern structural engineering. This article explores the future trends in this dynamic field, focusing on developments that promise to enhance efficiency, sustainability, and functionality in construction.
The Rise of Automation in Precast Manufacturing
Automation is set to revolutionize precast concrete production. Robotic systems and machine learning algorithms enhance precision, speed, and quality. Automated systems can streamline processes, from mixing ingredients to molding and curing concrete.
This shift toward automation minimizes human error and optimizes material usage. As a result, manufacturers can produce higher quantities of precast elements at competitive costs. The ongoing integration of Industry 4.0 technologies further supports this trend, creating smart factories equipped with advanced sensors and IoT devices.
Benefits of Automation
- Increased Efficiency: Automated systems significantly reduce production times.
- Quality Control: Continuous monitoring ensures consistent quality in products.
- Labor Cost Reduction: Less reliance on manual labor leads to lowered expenses.
Emphasis on Sustainability
The construction industry faces increasing pressure to adopt sustainable practices. Precast concrete technology is not exempt from this demand. Future trends indicate a greater emphasis on eco-friendly materials and methods.
For instance, manufacturers are exploring the use of recycled aggregates in mix designs. Furthermore, the development of low-carbon concrete is gaining traction. This type of concrete reduces greenhouse gas emissions, making precast elements more sustainable while meeting stringent environmental regulations.
Innovative Solutions for Waste Management
Another sustainability trend relates to effective waste management. Precast technology produces less on-site waste due to its off-site manufacturing processes. Additionally, advancements in recycling techniques are enabling the reuse of precast components, extending their lifecycle.
Integration with Digital Technologies
The future landscape of precast technology will increasingly involve digitalization. BIM (Building Information Modeling) and digital twins are prominent in this area. These technologies optimize design and construction processes through enhanced visualization and simulation capabilities.
Danish firm, for example, utilizes BIM to streamline its precast concrete projects. Digital modeling allows teams to identify potential issues early in the design phase, leading to more efficient workflows. With BIM, stakeholders can work collaboratively, seamlessly sharing information throughout project development.
Smart Precasting Facilities
Digital integration is driving the establishment of smart precasting facilities. These facilities employ data analytics to predict demand, optimize production schedules, and manage resources efficiently. Such capabilities improve the bottom line and minimize delays, ultimately benefiting clients and developers alike.
Advanced Structural Characteristics
As precast technology evolves, the structural characteristics of precast elements are also improving. Innovations such as ultra-high-performance concrete (UHPC) are gaining traction. UHPC boasts superior strength and durability compared to traditional concrete, making it ideal for demanding applications.
Utilizing UHPC allows for thinner elements while maintaining structural integrity. This capability is particularly beneficial in architecture, where aesthetic considerations are paramount. Lightweight precast panels reduce the load on support structures, facilitating innovative designs.
Enhanced Seismic Performance
Future precast designs are likely to incorporate enhanced seismic performance features. Research indicates that precast concrete structures can be designed to better withstand earthquake forces. Reinforcement techniques, such as post-tensioning and fiber reinforcement, are paving the way for safer buildings.
Customization and Modularization Trends
Another trend in precast technology focuses on customization and modularization. Clients increasingly seek tailored precast solutions that meet specific architectural requirements. Advances in manufacturing techniques enable greater flexibility in design while retaining the benefits of mass production.
Modular precast systems facilitate rapid assembly on-site, minimizing construction timelines. This approach is especially relevant in urban environments where time and space are constrained. Off-site fabrication allows components to be completed simultaneously, significantly accelerating project delivery.
Client-Centric Approaches
This trend underscores a shift towards client-centric approaches in construction. By working closely with clients, engineers and designers can develop solutions that balance aesthetics and function, leading to better project outcomes.
Impact of 3D Printing
3D printing’s impact on precast technology is becoming increasingly evident. Additive manufacturing allows for the precise fabrication of complex geometries that traditional methods may struggle to achieve. This technology can create mold components or even precast elements directly, paving the way for unprecedented design possibilities.
As concrete 3D printing progresses, it could significantly lower costs, reduce waste, and speed up delivery times. Future applications may include fully automated production lines where 3D printers work in conjunction with traditional precast systems.
Potential Challenges
Despite its advantages, 3D printing in precast technology presents challenges. Regulatory hurdles and material limitations require careful consideration. As the industry adapts, standards and guidelines will need to evolve to accommodate 3D-printed solutions.
Collaboration with Research Institutes
The future of precast concrete technology will likely involve closer collaboration with academic and research institutes. These partnerships can drive innovation by focusing on material science, structural integrity, and environmental impact.
Through research initiatives, new findings can be quickly translated into practical applications. This collaboration may facilitate the development of advanced materials and bonding agents, enhancing the performance and sustainability of precast products.
Education and Knowledge Transfer
Educational institutions play a crucial role in informing the next generation of engineers about emerging trends. Programs focused on advanced precast technology and sustainable design can equip students with the knowledge needed in this rapidly changing field.
Conclusion
Precast concrete technology is poised for significant advancements that will reshape the construction landscape. The trends discussed, including automation, sustainability, digital integration, and enhanced structural characteristics, highlight the potential for innovation in this sector.
As the industry prioritizes efficiency, customization, and smart solutions, precast technology will continue to rise in prominence within structural engineering. Companies that embrace these changes will be better positioned to meet the evolving demands of clients while promoting sustainable practices that benefit the environment.
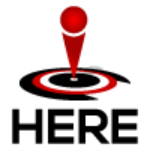